Body | Check this First:
Print quality issues often stem from confusion regarding ribbon and label compatibility. Specific materials require specific ribbons. Use these resources to confirm the installed ribbon is compatible with the specific material you are using:
Common Print Quality Issues, Causes and Resolutions
Repeated thin lined voids
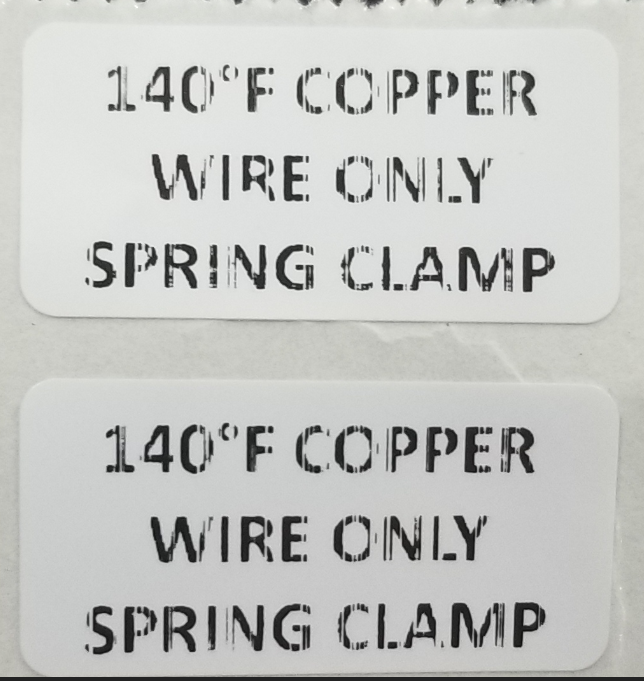
Repeated thin lines usually indicates mechanical failure of the print head. A THT print head is an array of pixels that heat up, this heat causes wax or resin on the ribbon to transfer to the label surface. Failed pixels cannot be repaired, the print heat must be replaced.
Pressure Indentation This is a common issue inherent to THT printing. When the printer is unused, the media is compressed between the platen roller and print head. Over time this pressure creates a thin line void. This line only occurs on the first label.
Smudges (Material age) Smudging indicates potential adhesive bleed from the label liner. This often occurs when materials are beyond shelf life or exposed to high heat or humidity. Material shelf life varies, with B-427 self-laminiating having one of the shortest at 1 year. Old ribbons can also produce poor print quality.
Garbled characters When text is garbled, overlaid, partially printed or jumbled together, this indicates some kind of communication interference. Try using a different connectivity method or PC to isolate the source of the issue (if using USB, try network connection and vice versa). Also make sure the printer is not connected to a USB splitter hub or laptop docking station - the printer should be connected to a USB port directly on the PC or laptop.
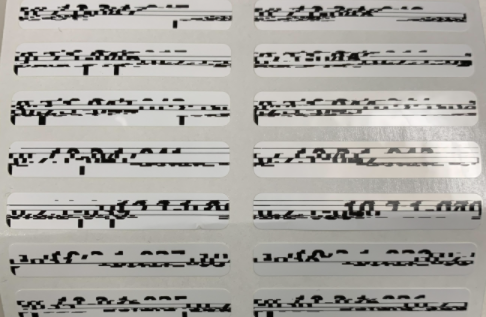 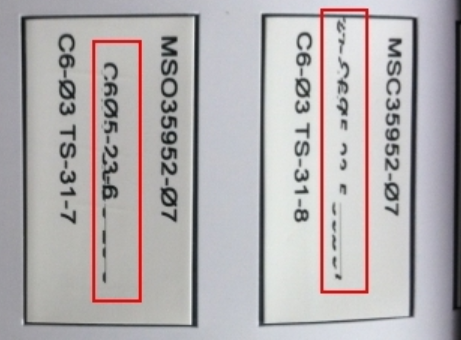 Faint print, light print, spotty print or no print No Print/Faded Print - Check the ribbon/label combination first. Do not proceed to additional troubleshooting until you confirm the ribbon series is compatible with the Brady material type loaded in your printer. Ribbon and Label Compatibility Make sure the ribbon hasn't been loaded upside down. Refer to your user manual or this knowledge base for instructions to load label and ribbon materials into your Brady printer.
Text Missing the Top or Bottom - If the text is missing the top or bottom of the letters and numbers on the label, the font size, font type or label size can be a factor. Possible letters and numbers for the top crossbar could be T, 7, 5, F, E.
Verify ribbon and label compatibility or clean the printer. Try another type of font or size of font if possible.Faded Print (Printer and Driver Settings) - Check the print head heat. This can be adjusted in the driver or in the printer menu. If a printer has multiple users, it's common for one coworker to make an adjustment without other users' knowledge. Reference your printer's user manual or articles in this knowledge base for information about print head heat adjustment for your Brady printer model.
Faded Print (Worn Platen Roller) - Check the platen roller for a gradual concave indentation. This is the roller mechanism that advances the labels on most Brady printer models. Normal wear on this component can cause poor label contact with the ribbon and print head. This component is field replaceable depending on your printer model.
Platen roller (green) on an i7100 printer
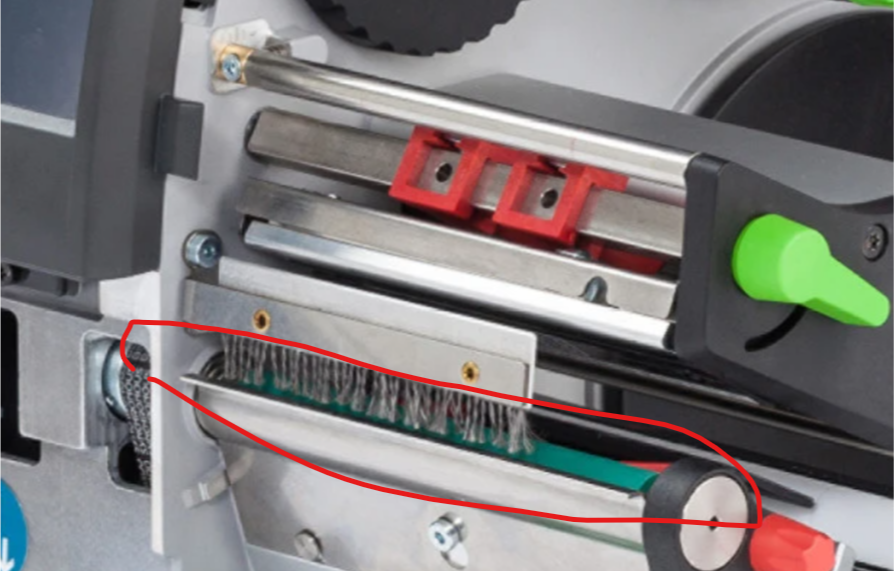
Spotty Print/Faded Print (Printhead Debris) - make sure the print head is clean. Adhesive residue and label debris can build up over time: Brady Thermal Printers - How to Clean/Extend the Life of Your Printhead Top Coat Issues (uncommon) - topcoat issues occur when there is a defect in the manufacturing process of the labels. This issue may be present across multiple rolls of label material that have the same lot number. You can rule out topcoat issues by loading a different label supply with a different lot and part number. Top coat may degrade for material beyond shelf life (material age).Ribbon Wrinkle - Curved voids across labels These curved voids occur when unequal tension is placed between the ribbon dispense and take up spool. Some Brady printers allow mechanical adjustments to correct ribbon wrinkle, however we don't recommend adjusting these settings unless you have extensive experience working with THT printers. Instructions in the article below are written for the i7100, however they apply to many THT printer models.
Offset Print (Too high, too low, left or right)First, make sure your printer is loaded correctly - this includes placement of sensors, label material and media guides. Reference this knowledge base or your printer user manual for proper media loading procedure. Some printer models allow adjusting print head pressure - this can can inconsistent print position. There are several methods to remediate issues related to the position of text and objects on the label. Reference this article to learn about these different configurations and when to use them.
If these articles do not resolve your issue, please take a picture if your print quality issue, include the ribbon and label part and lot numbers installed when the issue occurs and contact Global Brady Technical Support Contact Information. |
|
---|